CNC Rapid Prototyping: Revolutionizing Metal Fabrication
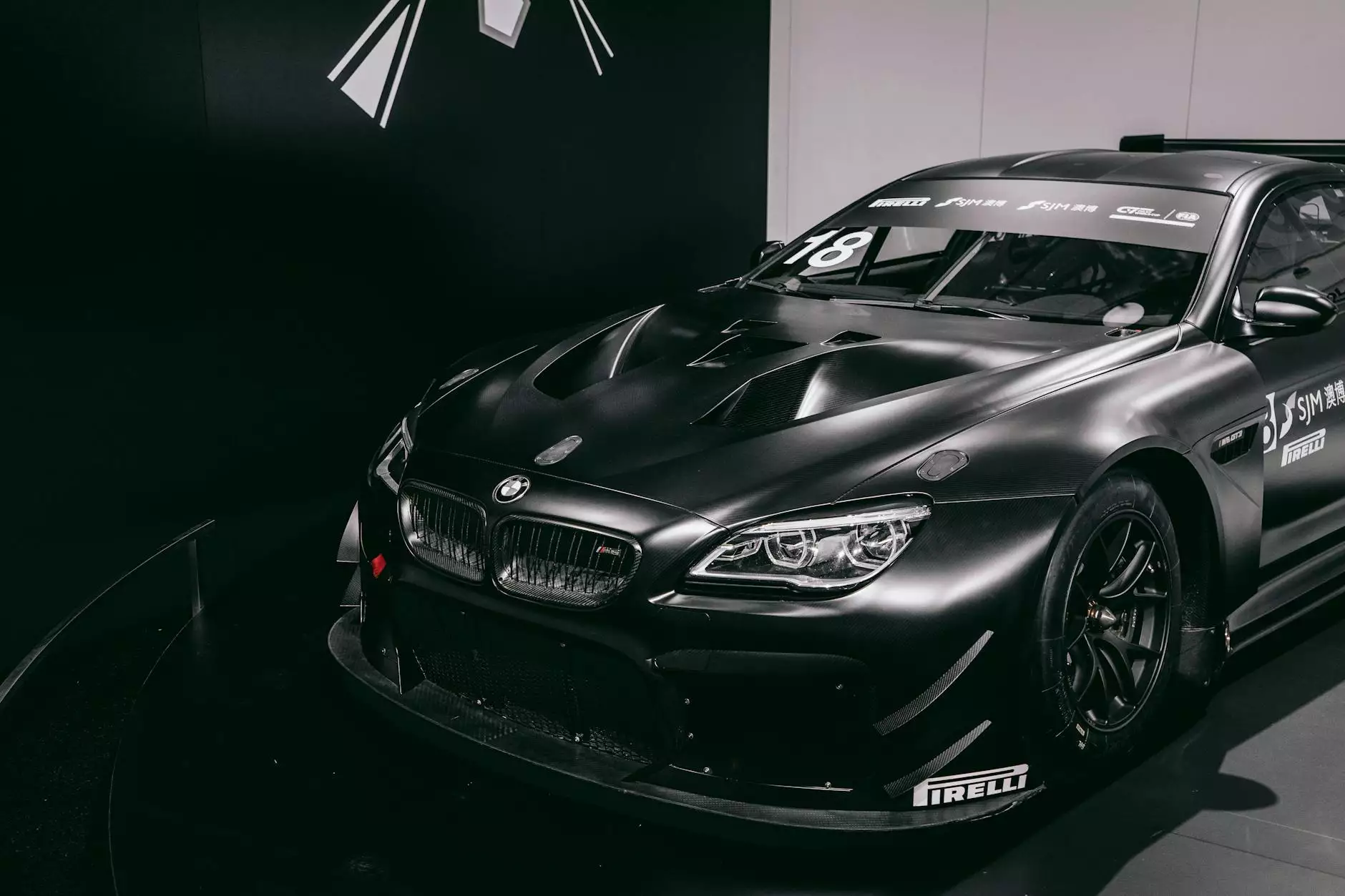
In today's fast-paced industrial landscape, businesses are continually seeking methods to enhance their manufacturing processes. One of the most groundbreaking advancements in this domain is cnc rapid prototyping. This innovative technique provides a plethora of benefits that can dramatically transform production cycles, reduce costs, and increase the quality of end products.
What is CNC Rapid Prototyping?
CNC rapid prototyping refers to the use of computer numerical control (CNC) technology to swiftly create prototypes from digital models. This process leverages 3D modeling software to design a part and then utilizes CNC machines to produce a physical representation of that part at an astonishing speed. This method is particularly advantageous in the field of metal fabrication, where precision and time efficiency are paramount.
Key Benefits of CNC Rapid Prototyping
The benefits of cnc rapid prototyping are numerous and multifaceted. Here are some of the most significant:
- Speed: The rapid production capabilities of CNC machines allow for quicker turnaround times. Prototypes that once required weeks to manufacture can now be completed in a matter of days, enabling businesses to accelerate their product development cycles.
- Precision: CNC machines boast remarkable accuracy, achieving tolerances as small as a few microns. This level of precision ensures that the prototype matches the digital model closely, minimizing the need for revisions.
- Cost-Effectiveness: By reducing material waste and labor costs, CNC rapid prototyping can be significantly more economical than traditional prototyping methods. This allows companies to allocate their resources more efficiently.
- Flexibility: The technology easily adapts to different designs and materials. Whether a prototype requires aluminum, steel, or other metals, CNC machines can handle the transition seamlessly.
- Enhanced Innovation: The fast prototyping cycle fosters a culture of innovation within organizations. Teams can brainstorm, test, and iterate designs quickly, leading to improved products that respond to market needs.
Applications of CNC Rapid Prototyping in Metal Fabrication
The implications of cnc rapid prototyping stretch far within the metal fabrication industry. Here are key applications:
1. Product Development
Companies can use CNC rapid prototyping to develop new products. From initial design concepts to final testing, the ability to produce functional prototypes swiftly ensures that engineers can identify and resolve potential issues early in the design process.
2. Customization
Manufacturers often face the challenge of designing products tailored to specific client requirements. CNC rapid prototyping allows for customized solutions that can be created quickly, thus providing competitive advantage through personalization.
3. Testing and Validation
Prototypes must undergo rigorous testing to validate their design. Rapid prototyping enables easy iterations based on testing feedback, ensuring that the final product meets necessary performance standards.
4. Tooling and Fixture Creation
Crafting tooling and fixtures for metal fabrication often requires precision components. CNC rapid prototyping streamlines the process, as engineers can quickly fabricate the necessary tools to maintain high productivity levels on the production floor.
5. Educational and Research Applications
In educational settings and advanced manufacturing research, cnc rapid prototyping provides hands-on learning experiences. Students and researchers can develop prototypes that will help them explore new materials and techniques.
The CNC Rapid Prototyping Process
Understanding the workflow of cnc rapid prototyping is crucial for businesses hoping to integrate this technology into their operations. Here is a comprehensive breakdown of the standard process:
Step 1: Design
The journey begins with the creation of a digital model using CAD (Computer-Aided Design) software. This software allows designers to develop detailed, 3D representations of their products.
Step 2: Converting the Design
Once the design is finalized, it is converted into a format compatible with CNC machines, typically using CAM (Computer-Aided Manufacturing) software. This step enhances the machine's ability to understand the specifications outlined in the CAD model.
Step 3: Material Selection
Choosing the right material is vital for prototyping success. Options can vary widely, including metals like aluminum, stainless steel, and titanium, each offering different strengths and properties.
Step 4: Machining
With the design converted and the material selected, the CNC machine begins the prototyping process. It cuts, mills, or shapes the material as per the predetermined specifications to create the prototype part.
Step 5: Post-processing
Once the machining is complete, some prototypes undergo finishing processes. These can include polishing, coating, or additional machining to ensure the part meets the desired visual and functional quality.
Step 6: Testing and Evaluation
Finally, the prototype is tested and assessed. If necessary, feedback is considered to refine the design further, and the cycle may repeat until the final product is achieved.
Challenges of CNC Rapid Prototyping
While the benefits of cnc rapid prototyping are substantial, the process does come with its own set of challenges:
- Initial Costs: The upfront investment for CNC machinery can be significant. However, the long-term savings often outweigh these initial expenses.
- Material Limitations: Not all materials are suitable for CNC rapid prototyping, which may constrain certain designs.
- Skill Requirements: Operating CNC machines and software requires specialized skills. Adequate training and resources must be allocated to ensure efficient use of technology.
The Future of CNC Rapid Prototyping in Metal Fabrication
As technology continues to evolve, the future of cnc rapid prototyping looks exceptionally promising. Following trends indicate its trajectory:
1. Integration with IoT
The integration of the Internet of Things (IoT) and CNC machines is set to revolutionize the field, allowing for real-time monitoring and optimization of the prototyping process.
2. Advancements in AI and Machine Learning
Artificial intelligence will enable CNC machines to learn from past projects, predicting potential hurdles and suggesting optimizations that enhance productivity and accuracy.
3. Sustainable Practices
As industries move towards sustainable practices, CNC rapid prototyping is likely to adopt eco-friendly materials and processes, contributing positively to environmental conservation efforts.
4. Greater Accessibility
As technology becomes more widespread, small to medium-sized enterprises will have increased access to CNC rapid prototyping, democratizing high-quality prototyping capabilities across industries.
Conclusion
In conclusion, cnc rapid prototyping stands as a pivotal advancement in the metal fabrication industry, addressing challenges related to speed, precision, and cost. By adopting this technology, businesses can drive innovation, enhance their production processes, and achieve a competitive edge in the market. As the landscape of manufacturing continues to shift, those who embrace CNC rapid prototyping will undoubtedly pave the way for future successes.
For further insights into CNC rapid prototyping and its integration into your business, visit Deep Mould, where expertise meets innovation in metal fabrication.