Understanding Plastic Injection Molders: A Pillar in Electronics and Medical Supplies
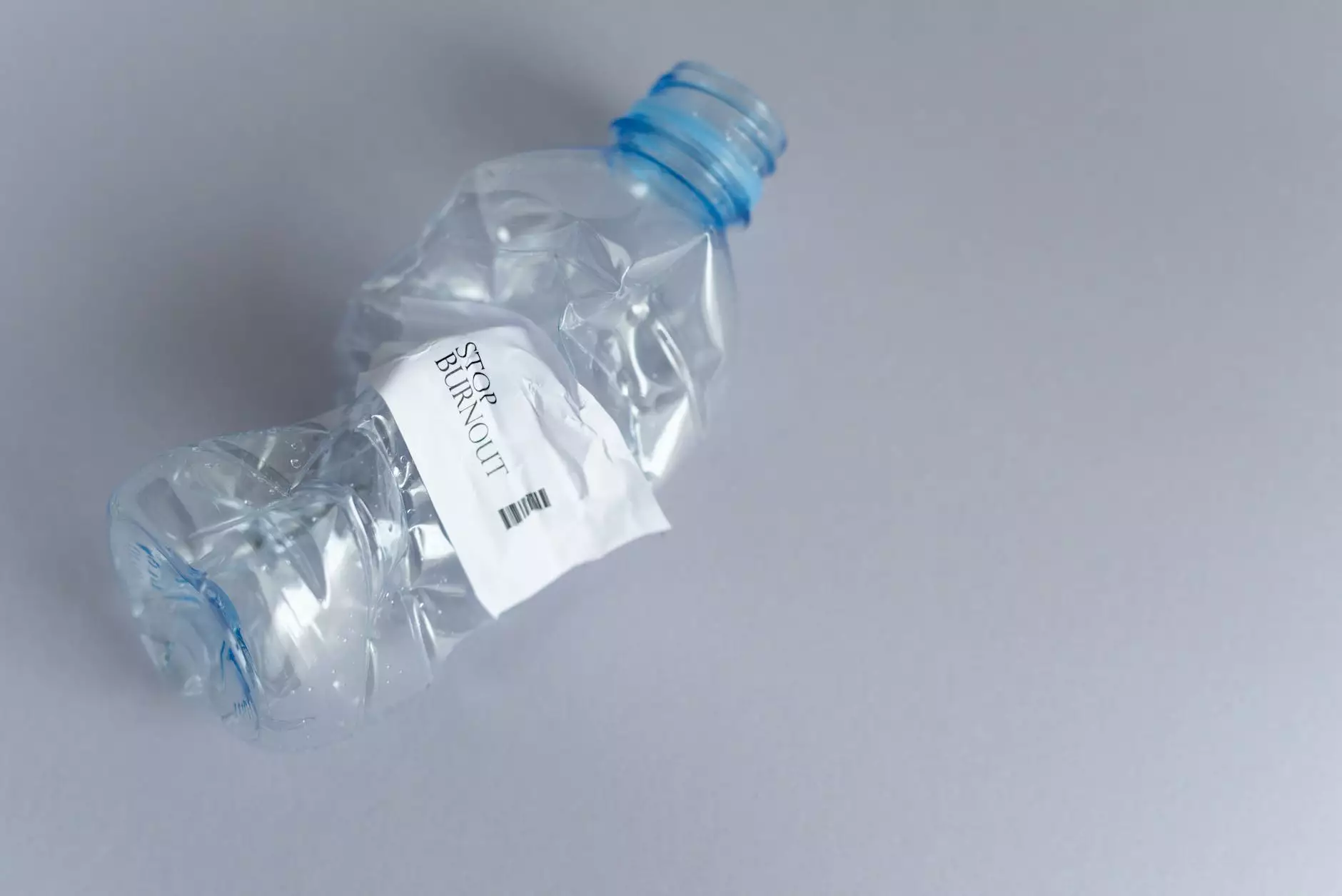
The modern manufacturing landscape is significantly influenced by the advancements in plastic injection molding. This process, integral to various industries, particularly electronics and medical supplies, provides countless benefits that enhance production efficiency and product quality. In this article, we will delve deeply into the world of plastic injection molders, examining their vital role and significance in today's market.
What Are Plastic Injection Molders?
Plastic injection molders are sophisticated machines that create parts and components by injecting molten plastic into molds. The process not only allows for high-volume production with minimal waste but also affords designers the flexibility to create complex shapes and sizes. This section will explore the various components and working mechanisms of plastic injection molders.
Components of Plastic Injection Molding Machines
- Injection Unit: The heart of the injection molding machine, where plastic pellets are heated and melted.
- Mold: A hollowed-out block that shapes the plastic as it cools and solidifies.
- Clamping Unit: This part holds the mold closed during the injection process to withstand the pressure of the molten plastic.
- Cooling System: Ensures the finished part cools uniformly to enhance strength and durability.
- Control System: Manages the operation of the machine, including temperature settings and cycle times.
The Injection Molding Process
The injection molding process involves several critical stages that are essential for ensuring high-quality outputs. Here’s a detailed breakdown of these stages:
1. Material Preparation
The first step involves selecting the appropriate type of plastic material based on the final product's requirements, including strength, flexibility, and heat resistance. Common materials used include thermoplastics like ABS, polycarbonate, and polystyrene.
2. Melting and Injection
Once the pellets are prepared, they are fed into the injection unit where they are heated until they reach a molten state. The molten plastic is then injected into the mold under high pressure to ensure it fills every cavity and detail.
3. Cooling
After the injection, the mold is cooled to allow the plastic to solidify. Proper cooling is crucial; it affects the part's dimensions and mechanical properties.
4. Ejection
After sufficient cooling, the mold opens and the finished part is ejected. This stage may include an ejector system that provides controlled force to remove the part without damaging it.
Significance of Plastic Injection Molders in Electronics
The electronics industry is characterized by rapid technological advancements which require innovative manufacturing processes. Plastic injection molders play a pivotal role in the production of various electronic components, including:
- Casings and Enclosures: Providing durable protection for electronic devices.
- Connector Parts: Creating precision components that ensure reliable electrical connections.
- Switches and Buttons: Producing ergonomic designs that enhance user experience.
The lightweight nature of plastic combined with the ability to create complex geometries makes injection-molded parts preferable for many electronic applications. This efficiency translates into faster product releases and increased market competitiveness for businesses, such as those found at Nolato.com.
The Impact of Plastic Injection Molders in Medical Supplies
The medical supplies sector demands high standards of quality and precision, where safety is paramount. Plastic injection molders contribute extensively by producing:
- Surgical Instruments: Ensuring reliability and durability through robust designs.
- Disposable Devices: Facilitating the production of single-use items essential for maintaining hygiene.
- Packaging: Crafting protective packaging for sensitive medical products.
The stringent regulations governing medical production mean that precision and compliance in the manufacturing process are non-negotiable. Plastic injection molding provides companies like Nolato with the ability to maintain these standards while catering to high-volume demands.
Benefits of Using Plastic Injection Molding
In both the electronics and medical supply industries, the advantages of plastic injection molding are manifest. Here are some key benefits:
1. Efficiency and Speed
Plastic injection molding is an efficient process, allowing for the rapid production of high volumes of parts without compromising on quality. Cycle times can be minimized, which is essential for companies looking to meet tight deadlines.
2. Design Flexibility
Designers can create intricate shapes and complex geometries that would be challenging or impossible with other manufacturing methods. This flexibility encourages innovation in product development.
3. Reduced Waste
Injection molding is a highly efficient process that maximizes material use and minimizes waste. Excess plastic can often be recycled and reused, aligning with sustainability goals.
4. Consistency in Quality
Once the mold is created, the injection process can consistently produce parts that meet accurate specifications. This reliability is particularly crucial in the medical field, where even minor variations can lead to significant implications.
Best Practices for Successful Plastic Injection Molding
For businesses to leverage the full potential of plastic injection molding, adhering to best practices is essential:
1. Material Selection
Choosing the right plastic material is critical. Factors such as strength, thermal properties, and intended application should dictate material choice.
2. Mold Design
A well-designed mold maximizes efficiency and minimizes defects. Consideration must be given to part geometry, wall thickness, and ejection mechanisms.
3. Process Optimization
Regularly reviewing and optimizing the injection molding parameters will lead to improved cycle times and reduced material usage while maintaining part quality.
4. Quality Control
Implementing robust quality control measures throughout the production process ensures that all parts meet the requisite specifications and standards.
The Future of Plastic Injection Molding
As technological innovations continue to evolve, so too will the plastic injection molding industry. The integration of automation and smart manufacturing technologies will likely streamline processes further, enhance product quality, and lower production costs. Additionally, advancements in sustainable materials will align the industry with global environmental goals, allowing manufacturers to produce eco-friendly products without sacrificing performance.
Conclusion
The impact of plastic injection molders in industries such as electronics and medical supplies cannot be overstated. These machines not only enhance production capabilities but also provide the flexibility and precision required to meet stringent industry standards. Companies like Nolato exemplify the advantages of leveraging advanced injection molding technologies to stay competitive in a rapidly evolving market.
In summary, embracing the capabilities of plastic injection molding is essential for businesses aiming for growth and sustainability. As we move towards a future defined by continuous innovation, the reliance on proficient plastic injection molders will only intensify, making it a fundamental aspect of modern manufacturing.